Generally, for synthetic drugs, they are crystallized in an organic solvent. At the same time, they contain a large amount of organic solvents. If these solvents are directly discharged into the atmosphere, it will not only seriously pollute the environment, but also cause energy waste. Therefore, it is in line with the requirements of environmental protection and enterprise development to recover and recover various solvents from raw materials and drugs when drying them. Therefore, for the drying of APIs and some drugs, it is more appropriate to choose a closed-loop drying system. The system is helpful to realize more effective unification of economic benefits, environmental benefits and social benefits.
Advantages Compared With Traditional Drying Equipment
It can effectively recover organic solvent, reduce production cost and avoid environmental pollution caused by solvent.
It allows the material to be dried at a low moisture content (the moisture content can be reduced to 0.5%) at a low temperature of the drying medium (usually nitrogen).
During the drying process of the closed-circuit circulating fluidized bed dryer, the hot and humid air containing the solvent enters the condenser to make the solvent in the air become liquid. In this way, not only the solvent can be recovered, but also the air can be condensed, dehumidified and dried. The recovered solvent can be reused to save cost. At the same time, the discharged air will not cause pollution to the environment. After condensation dehumidification, the absolute humidity in the air is low, and the drying capacity of the dryer becomes strong. It is more suitable for moisture absorption and drying of materials in closed-circuit circulating fluidized bed dryer. During the drying process of the closed-circuit circulating fluidized bed dryer, the hot and humid air containing the solvent enters the condenser to make the solvent in the air become liquid. In this way, not only the solvent can be recovered, but also the air can be condensed, dehumidified and dried. The recovered solvent can be reused to save cost. At the same time, the discharged air will not cause pollution to the environment. After condensation dehumidification, the absolute humidity in the air is low, and the drying capacity of the dryer becomes strong. It is more suitable for moisture absorption and drying of materials in closed-circuit circulating fluidized bed dryer.
The closed loop circulating fluidized bed dryer is a fully enclosed structure. The circulating air inside the machine is nitrogen. When drying anaerobic materials or materials containing flammable and explosive organic solvents, the materials in the dryer cannot be burned or oxidized due to the low oxygen in the circulating air. In this way, the system effectively avoids fire or explosion accidents in the production process, and the safety level is high.
When the sealed loop circulating fluidized dryer works under the condition of only slight positive pressure, the internal pressure needs to be low. Therefore, the device is equipped with a relatively low fan power. Under positive pressure, hot air is blown out from the bottom of the material mesh plate. Strong air penetration ability. Although the fluidization height of the material is not high, the hot air contacts the material more fully and the drying speed is faster. At the same time, the energy consumption is reduced.
The main machine of the closed-circuit circulating fluidized bed dryer adopts a special pulse back blowing dust removal system. Good dust removal effect. The filter element is made of special materials, with good surface finish, large filtration area, high filtration accuracy and low resistance. In this case, dust is not easily attached to the filter cartridge, but it is easy to disassemble and clean.
Principle
1. Nitrogen filling and oxygen discharge
When the corresponding pipeline control valve is closed, the system is fully closed; When the exhaust pump is turned on, the oxygen in the system will be pumped out to make the system reach the micro negative pressure state. When the system pressure gauge shows a certain value, close the corresponding exhaust valve and exhaust pump. At this time, the nitrogen control valve is opened and nitrogen is injected into the system. When the residual oxygen in the system is less than the required value detected by the online oxygen detection device, the system is in a micro positive pressure state. At this time, close the nitrogen control valve and enter the next process.
2. Drying period
Open the circulating fan to make the material flow well; Turn on the radiator and heat the system to the required temperature. Through nitrogen transfer, heat takes away the water, organic solvent and a small amount of micro powder in the material. In this system, fine powder is collected by a dust collector (filtered to 2-5 μ m)。 After passing through the condenser, the solvent and organic solvent in the air are condensed into liquid and collected by the storage tank. After dehumidification and condensation, the nitrogen becomes dry and circulates in the system through the fan.
3. Nitrogen protection system
Nitrogen protection is mainly controlled by online oxygen detector. When the oxygen content exceeds the required value, the nitrogen filling device is automatically opened to fill nitrogen into the system. When the oxygen content of the system meets the requirements, the nitrogen charging device will automatically close.
4. Overpressure protection system
When the pressure in the system exceeds the set value, the pressure detection device acts and automatically empties and releases the pressure. When the system pressure meets the requirements, close the automatic exhaust valve and the system operates normally.
Technical Parameters
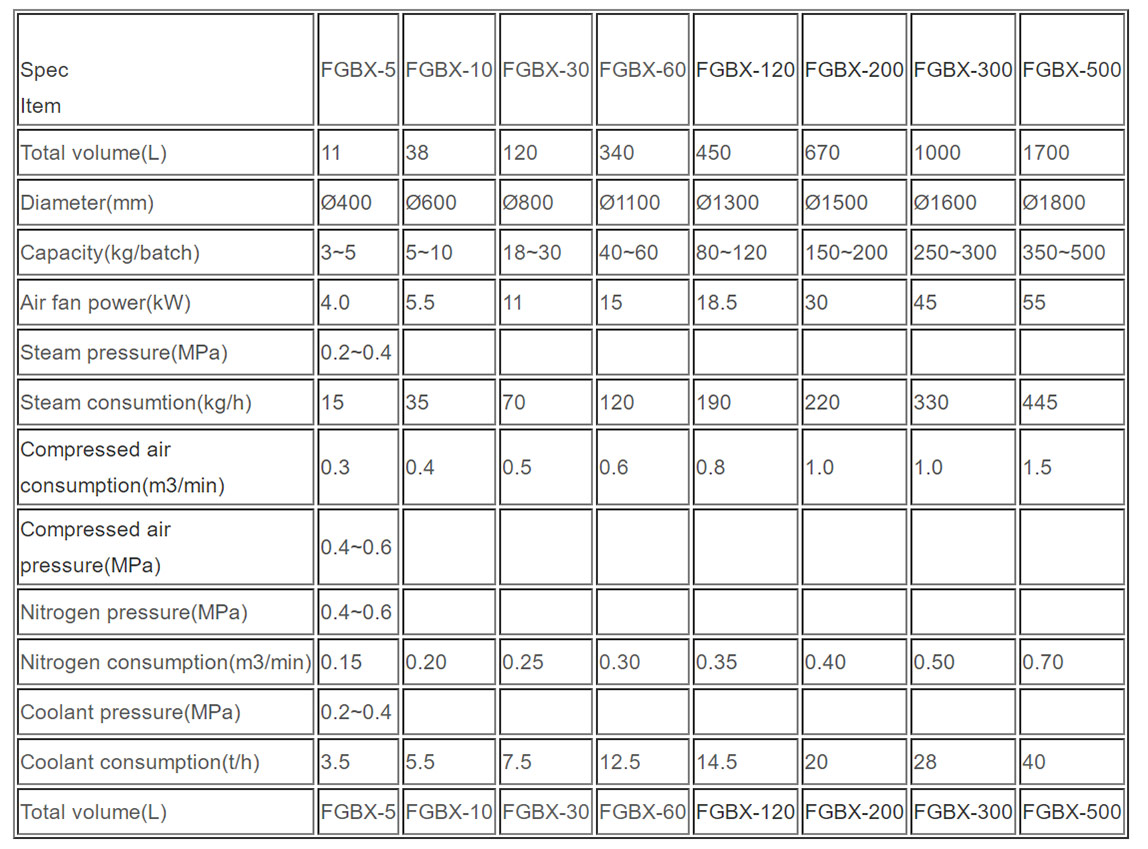